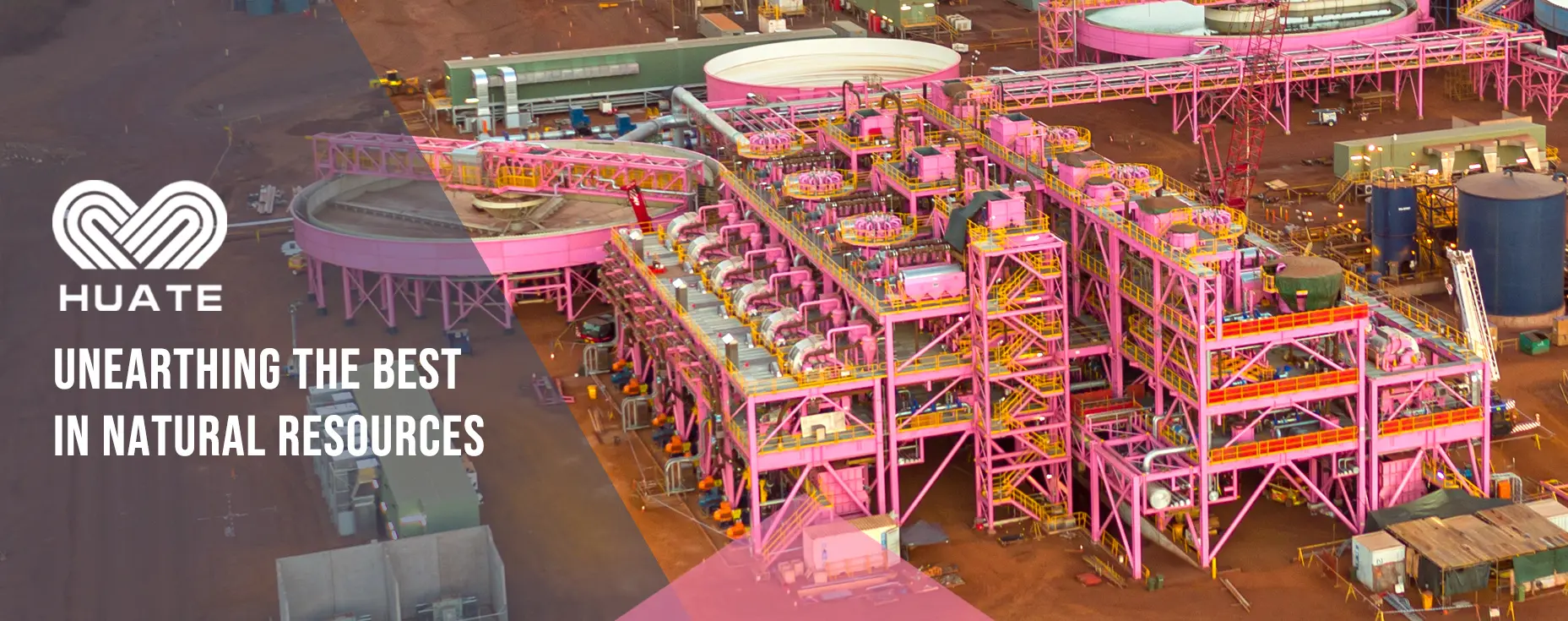
Como un dos metais máis antigos e máis utilizados no mundo, o mineral de ferro é unha materia prima esencial para a produción de ferro e aceiro.Actualmente, os recursos de mineral de ferro están esgotando, caracterizado por unha maior proporción de mineral magro en comparación co mineral rico, o mineral máis asociado e as composicións complexas de mineral.O ferro extrae habitualmente do seu mineral, coñecido como hematita ou magnetita, mediante un proceso chamado beneficio do mineral de ferro.Os pasos específicos implicados na extracción industrial de ferro poden variar dependendo da natureza do mineral e dos produtos desexados, pero o proceso xeral normalmente implica as seguintes etapas:
Minería
Os depósitos de mineral de ferro identifícanse primeiro mediante actividades de exploración.Unha vez que se atopa un depósito viable, o mineral extráese do terreo mediante técnicas mineiras como a minería a ceo aberto ou subterránea.Esta fase inicial é crucial xa que prepara o escenario para os procesos de extracción posteriores.
Trituración e moenda
A continuación, o mineral extraído tritúrase en anacos máis pequenos para facilitar o procesamento posterior.A trituración adoita realizarse mediante trituradoras de mandíbula ou trituradoras de cono, e a moenda realízase mediante molinos autóxenos ou molinos de bolas.Este proceso reduce o mineral a un po fino, facilitando a súa manipulación e procesamento nas etapas posteriores.
Separación magnética
O mineral de ferro contén moitas veces impurezas ou outros minerais que deben ser eliminados antes de que se poida utilizar na produción de ferro e aceiro.A separación magnética é un método común empregado para separar minerais magnéticos dos non magnéticos.Os imáns fortes, como o separador de imáns Huate, úsanse para atraer e separar as partículas de mineral de ferro da ganga (materiais non desexados).Este paso é fundamental para mellorar a pureza do mineral.
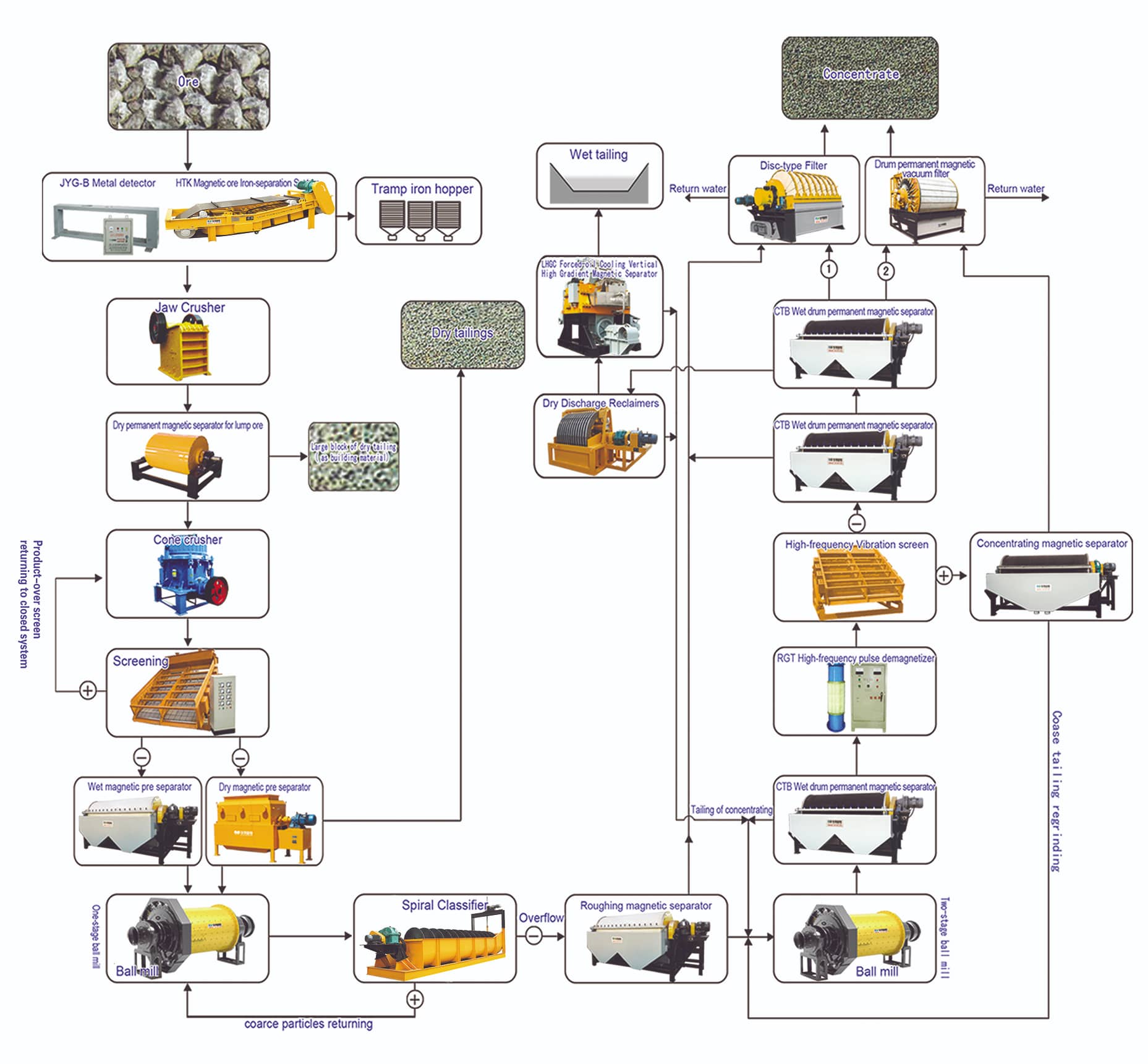
Beneficio
O seguinte paso é o beneficio do mineral, onde o obxectivo é aumentar o contido de ferro mediante diversas técnicas.Este proceso pode implicar métodos de lavado, cribado e separación por gravidade para eliminar as impurezas e mellorar a calidade do mineral.O beneficio tamén pode incluír a flotación, onde se engaden produtos químicos ao mineral para facer que as partículas de ferro floten e se separen do resto do material.
Pelletización o Sinterización
Unha vez que o mineral foi beneficiado, pode ser necesario aglomerar as partículas finas noutras máis grandes para un procesamento máis eficiente.A peletización consiste en formar pequenos gránulos esféricos facendo caer o mineral con aditivos como pedra caliza, bentonita ou dolomita.A sinterización, por outra banda, implica quentar os finos do mineral xunto con fluxos e brisa de coque para formar unha masa semifundida coñecida como sinterización.Estes procesos preparan o mineral para a fase final de extracción mellorando as súas propiedades físicas e as súas características de manipulación.
Fundición
O paso final do proceso de extracción é a fundición, onde o mineral de ferro quentase nun alto forno xunto co coque (combustible carbonoso) e caliza (que actúa como fundente).A intensa calor descompón o mineral en ferro fundido, que se recolle no fondo do forno, e escoura, que flota enriba e se elimina.O ferro fundido é posteriormente fundido en varias formas, como lingotes ou tochos, e procesado posteriormente para obter os produtos de ferro e aceiro desexados.
É importante ter en conta que os diferentes depósitos de mineral de ferro e plantas de procesamento poden ter variacións nos procesos específicos empregados, pero os principios xerais seguen sendo similares.A extracción de ferro do mineral é un proceso complexo e de varios pasos que require unha coidadosa xestión dos recursos e da tecnoloxía.A inclusión de equipos avanzados como o separador magnético Huate mellora a eficiencia e calidade do proceso de separación, garantindo que o produto final cumpra os estándares esixidos para a produción de ferro e aceiro.
Hora de publicación: 08-Xul-2024